Unique Design
The Crown Model III is a Continuous Loop, Shallow Bed Extractor and is extremely reliable and forgiving even under adverse conditions.
It offers the benefits of lower power requirements, excellent component life, ease of operation and the capability of higher operating capacities. The Crown continuous loop, shallow bed design is the most efficient of several methods of extracting vegetable oils from oil-bearing seeds. It performs by dissolving oil from the prepared material with solvent and is capable of processing a wide variety of products.
Points to Remember
- Over 250 Crown Extractors installed worldwide.
- Excellent reliability and safety record.
- Proven design - over 50 years of reliable operation, backed by a company established in1878.
- A daily capacity of up to 8,000 rated tons per day of suitably prepared soybeans per extractor.
- Also available in modular, pre-piped, skid mounted units for smaller capacities.
- Extractors will operate continually on a wide range other commercially significant oilseeds and nuts either directly or when processing cake or collets from a prepress or expander section.
Advantages of the Crown Extractor
- Unique, shallow, wide and long flake bed promotes excellent solvent contact, percolation and rapid drainage allowing more complete extraction for the widest possible range of products.
- Expanders are not generally required to promote drainage as are necessary in deep bed extractors.
- Flake bed is turned completely over - allows solvent to contact flakes from all sides.
- Uniform, low solvent carry over to the DT saves energy. Self-cleaning drainage screens - stationary, vee-bar screens are wiped clean by the continuously moving bed of material.
- Completely automatic control of miscella reservoir levels.
- Constant volume of hexane in process.
- Incline of chain before discharge eliminates possibility of solvent overflow to DT.
- Overflow to reservoirs controls bed surface flooding caused by poor material discharge.
- Continuous discharge of flakes improves desolventiser performance.
- Extremely low 'fines' generation throughout the process.
- Easy to assemble, expand or relocate.
Points to remember
- Keeps running under adverse conditions.
- Long Life components especially simple internal chain.
- No internal baskets or moving screens.
- Excellent visibility and access.
- Seldom need to enter the machine for maintenance.
Process Description
Material is fed into the extractor via safety slide valves through the inlet hopper. This incorporates a level sensor device to automatically match the extractor speed with material input.The Model III shares the long proven automatic level control system that has been one of the major operating advantages of all Crown extractors. This system is especially effective when used with computer systems as an accurate "feed-forward" capacity signal used in control.
The material forms a uniform shallow bed and is washed with miscella coming in from the recycle pumps as it is conveyed across the upper, horizontal section of the extractor, counter current to the miscella.The concentrated miscella discharges from the extractor through a hydroclone. The hydroclone "scrubs" the fines from the oil/solvent mix before being pumped further to the distillation system. On a typical extractor there are seven stages of miscella ranging from about 2% oil concentration to full miscella of approximately 25%.
The material bed continues along to the curved tail "Loop" section where it is completely turned over with each particle washed from all sides to maximize extraction efficiency. As it resumes its horizontal journey, the bed is washed by miscella of reducing concentration until the series of fresh solvent washes in the lower horizontal section of the extractor.
Before leaving the Model III the material passes over a fine drainage area and inclined discharge area eliminating the possibility of solvent carryover to the Desolventiser-Toaster (DT). Also, the continuous discharge inherent in this design eliminates the possibility of steam entering from the DT which might cause screen corrosion or poor drainage.
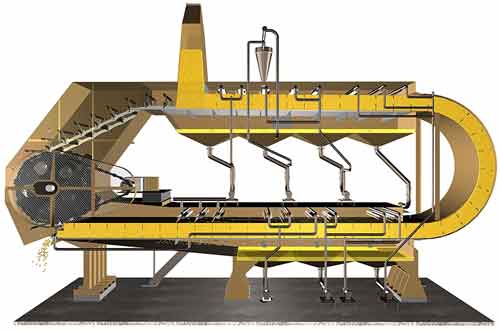
Equipment Brochure |